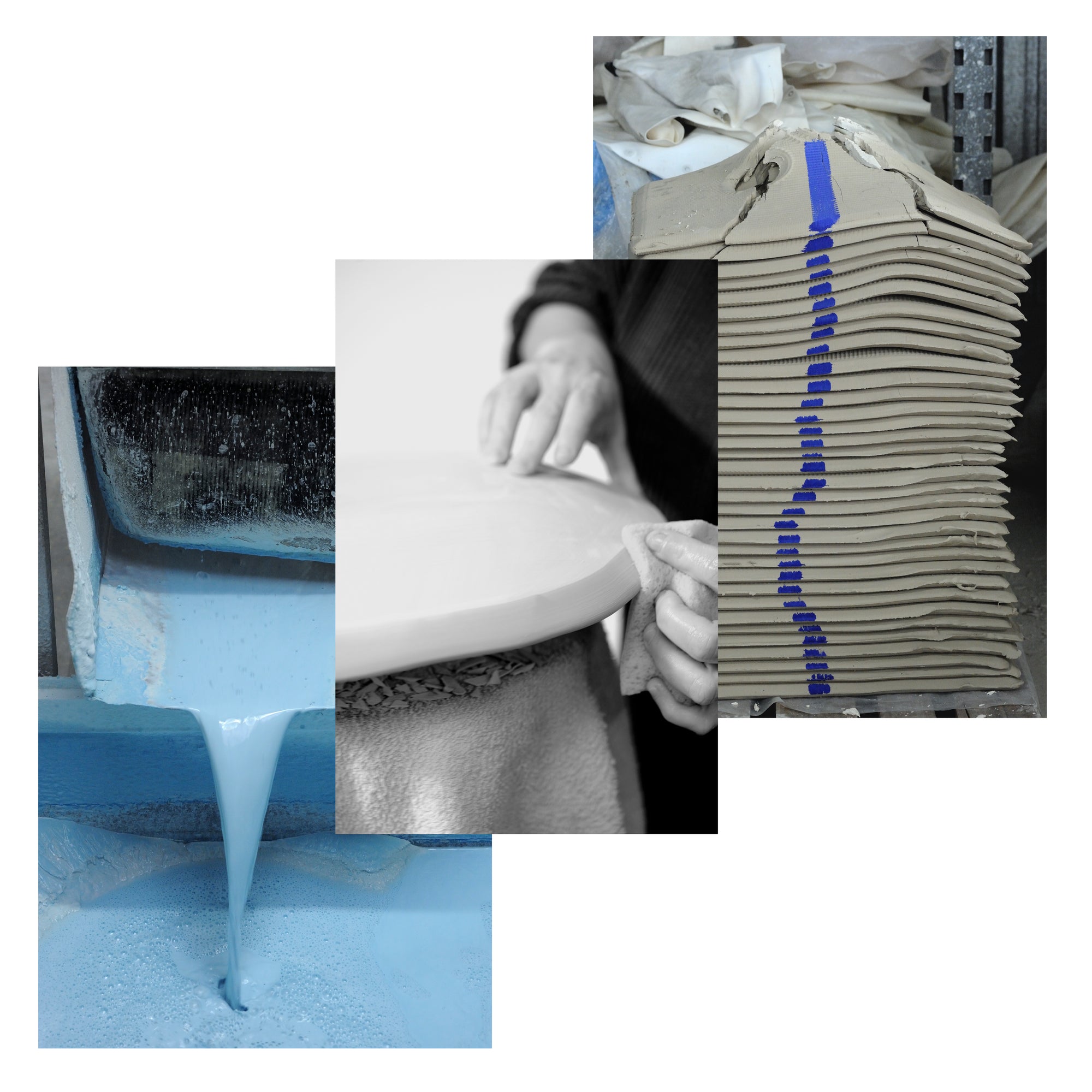
handmade
At Jars all our making, glazing, finishing and handling, and know-how of the material and even its hazards are the basics of a long learning process. Our hand-made skills are evident throughout:
In making a perfectly refined clay mix.
In casting the pieces.
In sponging and fettling edges and rims.
In applying the colored glaze.
In stacking ware in the kilns and taking it out.
For sorting by touch, feel and sight to control quality. So many of these workshop secrets are proudly shared between one ceramicist.
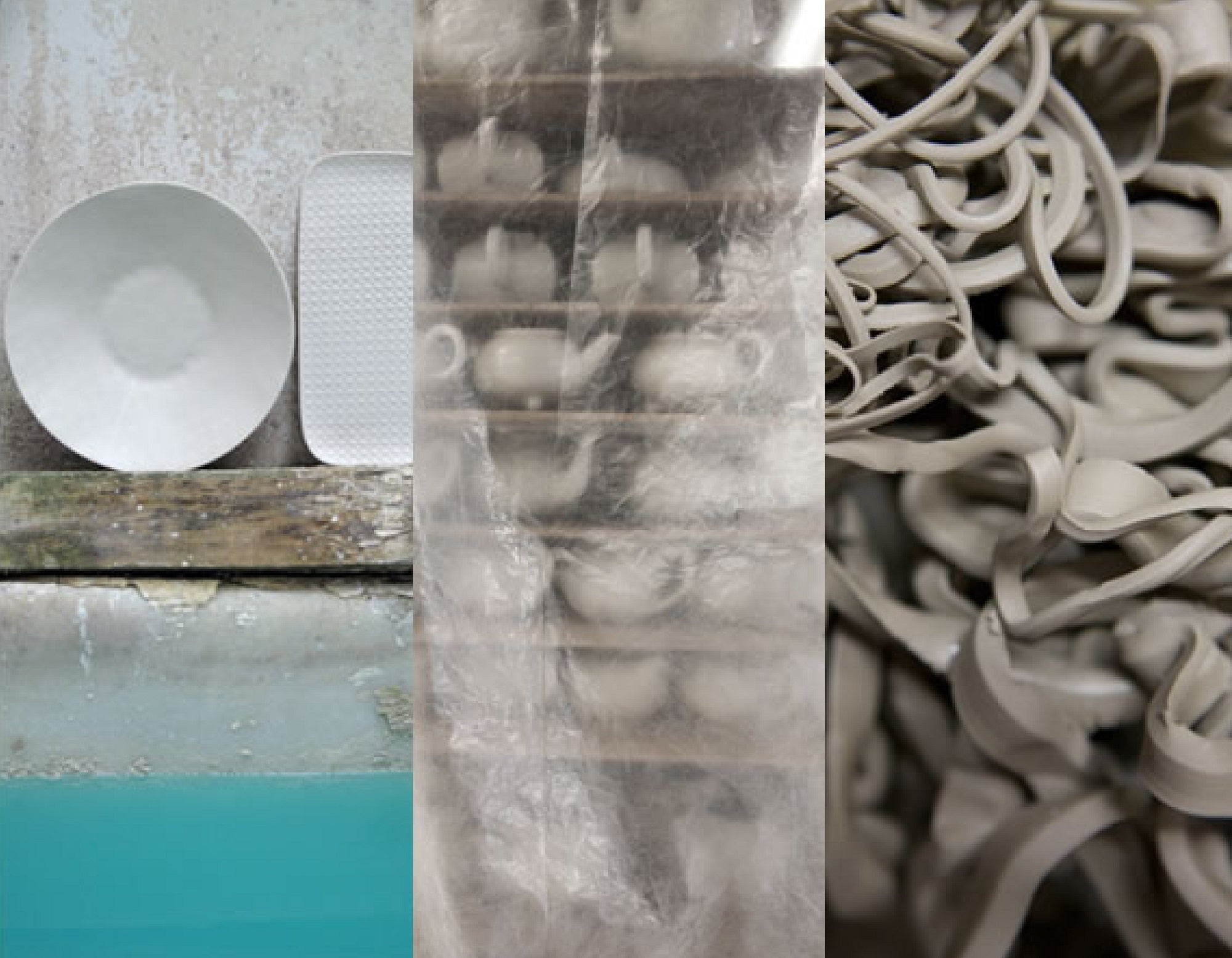
material
During this ‘grand feu’ firing at 2850F, the clays that make up its refined body become vitrified (the state at which the china and glaze melts and fuses together to form non-porous ware) and allows stoneware to reach the status of ‘noble ceramic”.
We could list all the reasons why stoneware gets this distinction but this would be long but it is unique to Jars. It is certainly the most resistant and the most natural ceramic material.
Thanks to this high fire and vitrification process stoneware recalls how rock was formed some millions of years ago with the trilogy of “earth, water and fire”.
As if it was a living thing stoneware comes from nature and returns to it.
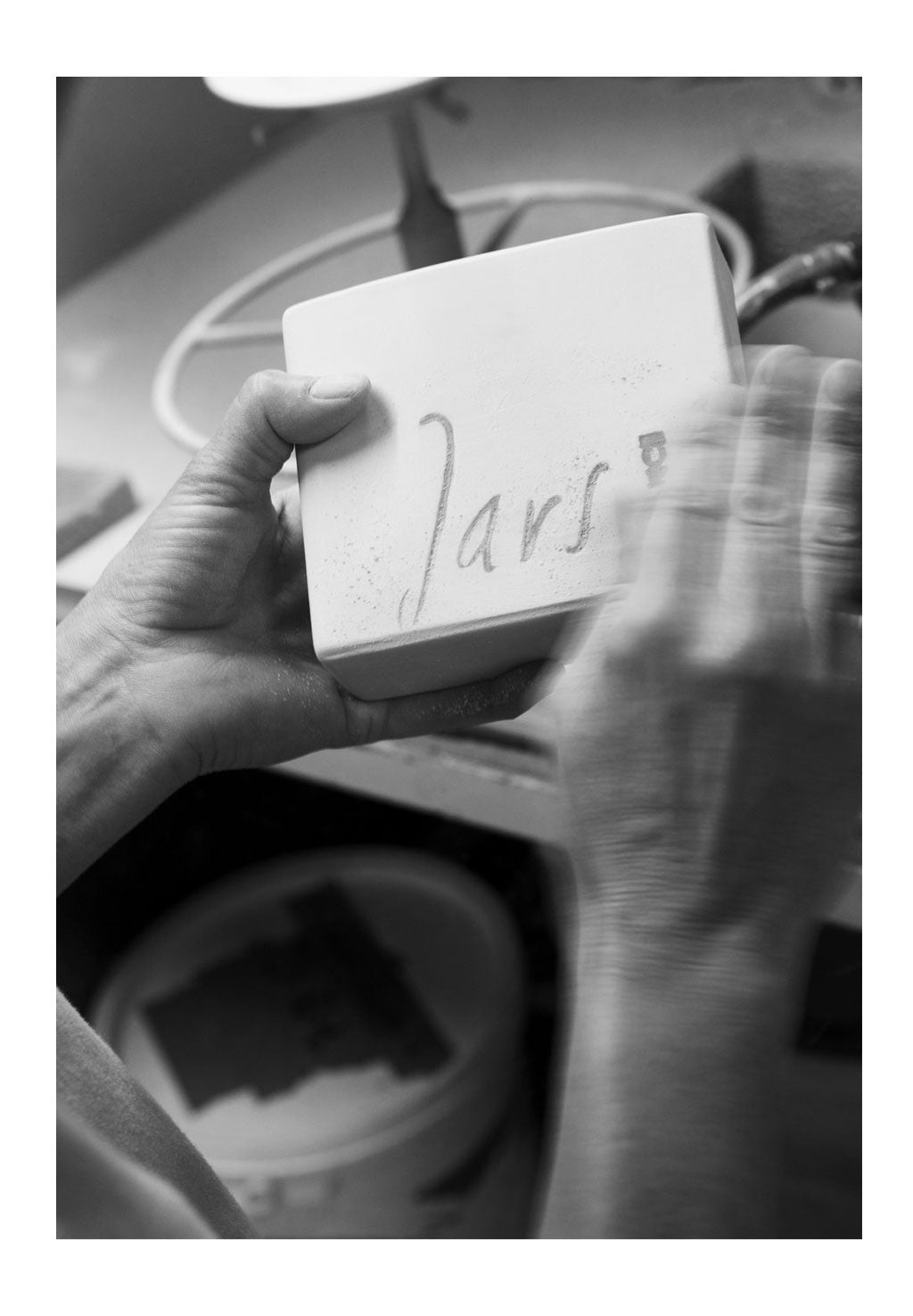
luxury of time
Imagining meaningful objects that defy aging. The art of taking time. To create, to shape, to take care of every detail. To convey that emotion that makes objects alive. This little extra soul that gives such a sweet fragrance to everyday life. The happiness of collecting durable and endearing objects, which transmit this love of timelessness. Of sharing one’s table, living intensely, inventing and reinventing the object. Giving it longevity. A sincere desire of coherence.
Sustainability & responsibility. Placing the planet as much as the human at the heart of our choices. Aware of the importance of each small action that adds up. Art of time. Art of living.
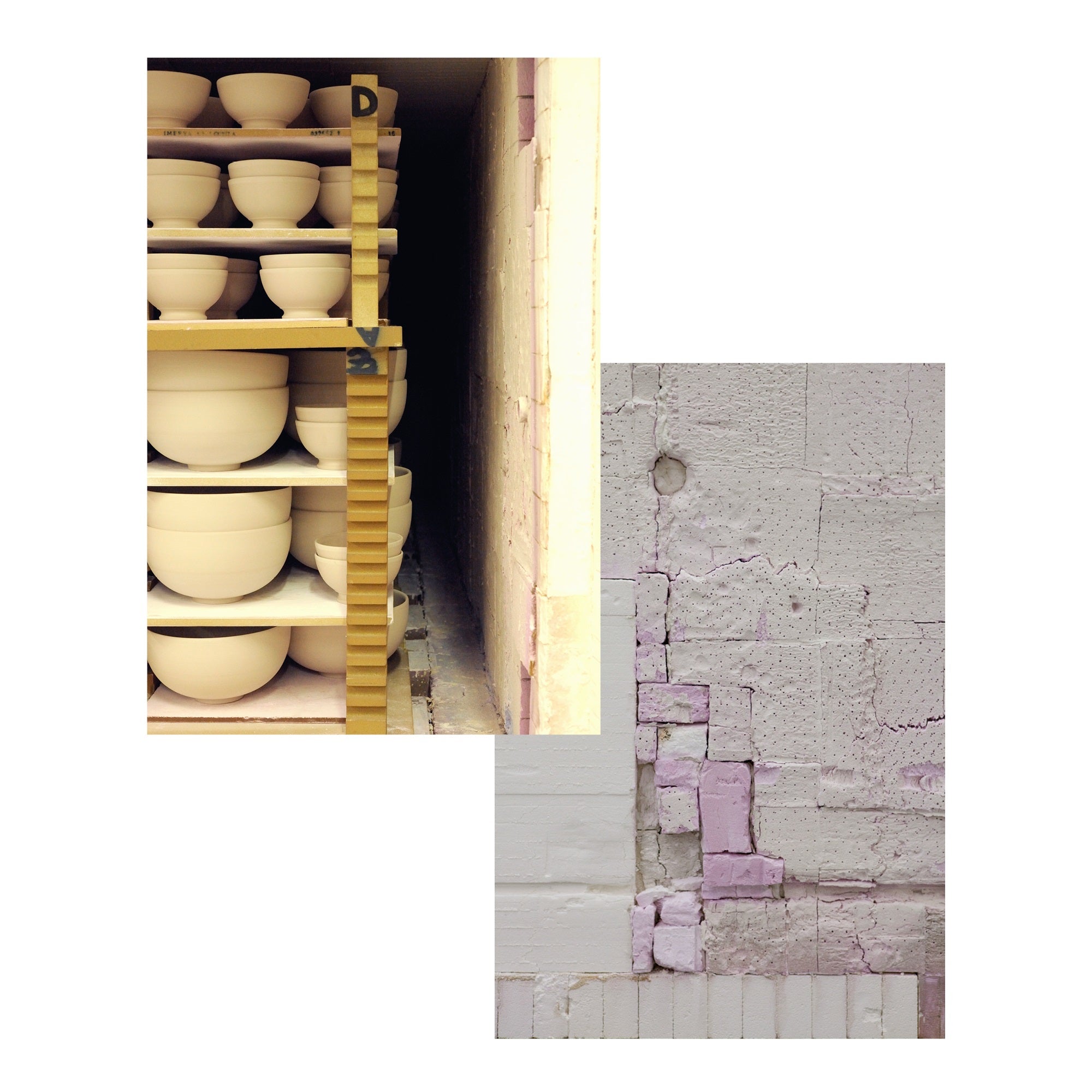
from raw to fired
When kilns reach ‘grand feu’, their peak temperature at 2850F, the item in raw stoneware is transformed into its final shape and into the world of color.
In all circumstances, the fire is the key player in how the final shape, or misshape even, of each batch turned out of the kiln. It decides which nuance of colors result from the glazes combining and interacting with each other, a true alchemy in fact.
In the early hours, when opening the kiln, the magic is revealed. Satisfaction or disappointment of the ceramicists… Each item is unique :”not completely the same, not really different.” And we kind of know why.
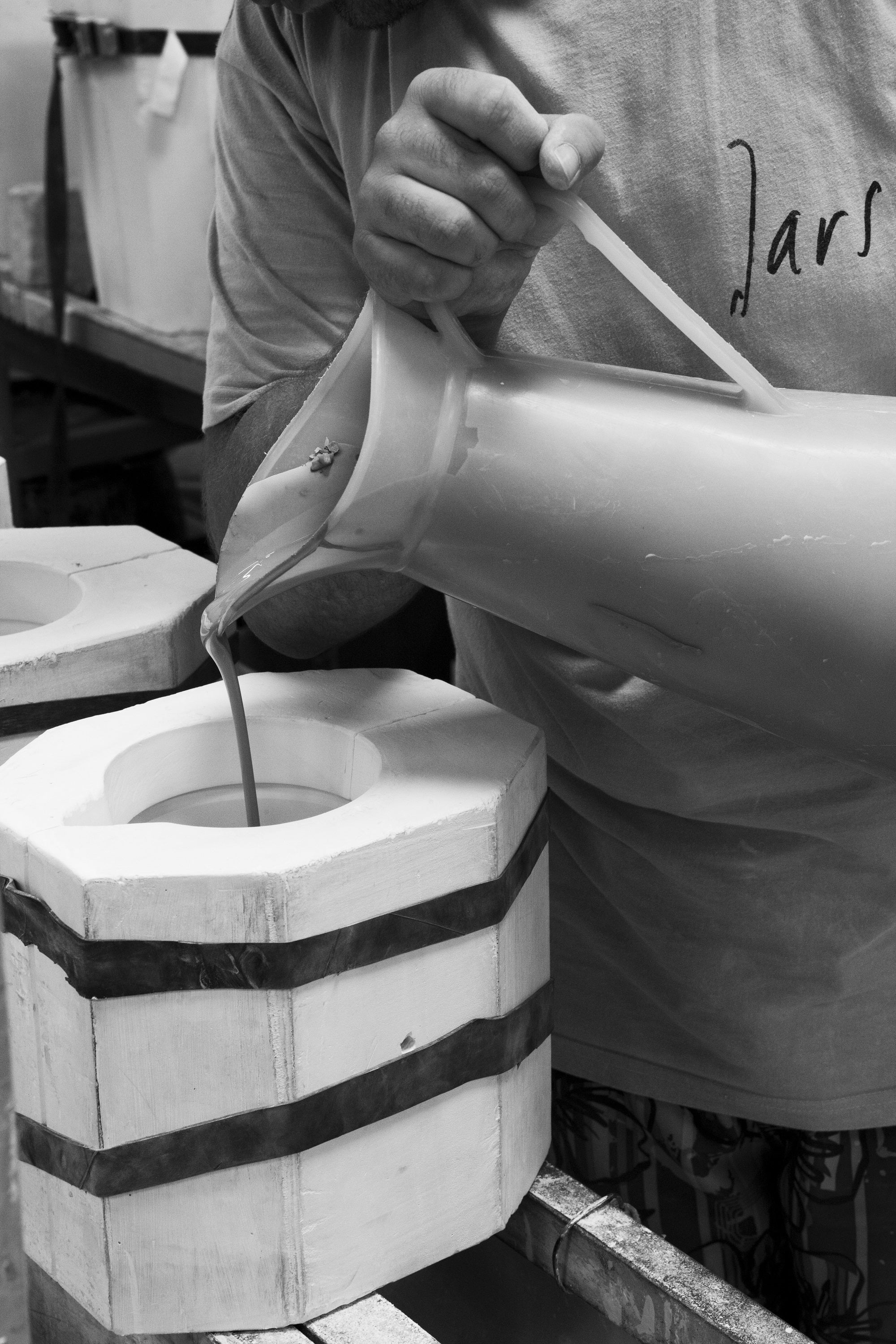
EPV label: the excellence of French know-how
The Entreprise du Patrimoine Vivant (EPV) label is a mark of recognition of the French State, put in place to reward French firms for the excellence of their traditional know-how.
The EPV State label brings together 1 400 French companies. It rewards a rare, renowned or ancestral know-how in the field of crafts and industry, for companies that are committed to maintaining their production activity in France.
In our workshops, 80 ceramists with artisanal know-how, guarantee the learning of the gestures and the transmission of workshops secrets and techniques from generation to generation, having raised Jars to the rank of the EPV label.
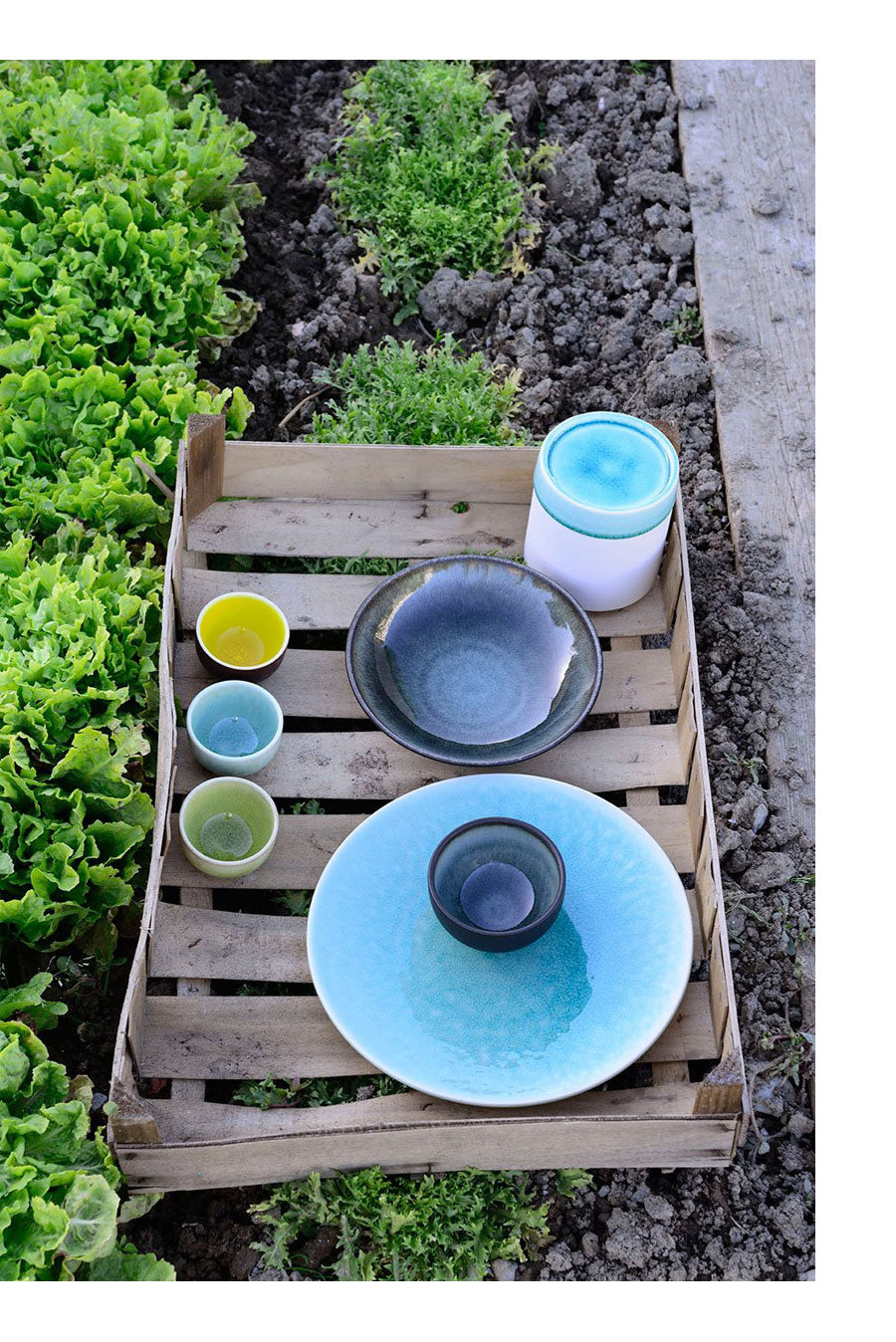
beautiful, functional & sustainable
An eco-responsible approach, daily & in our workshops. Surplus materials, water and paste, as well as the heat of our ovens are reused in the workshops. Exclusively constituted of natural materials, without lead and cadmium, our pieces are safe for the planet, and for you.